Microelectronics for military lead: Tresky presents robust DIE bonding and fiber optic technologies for modern defense systems
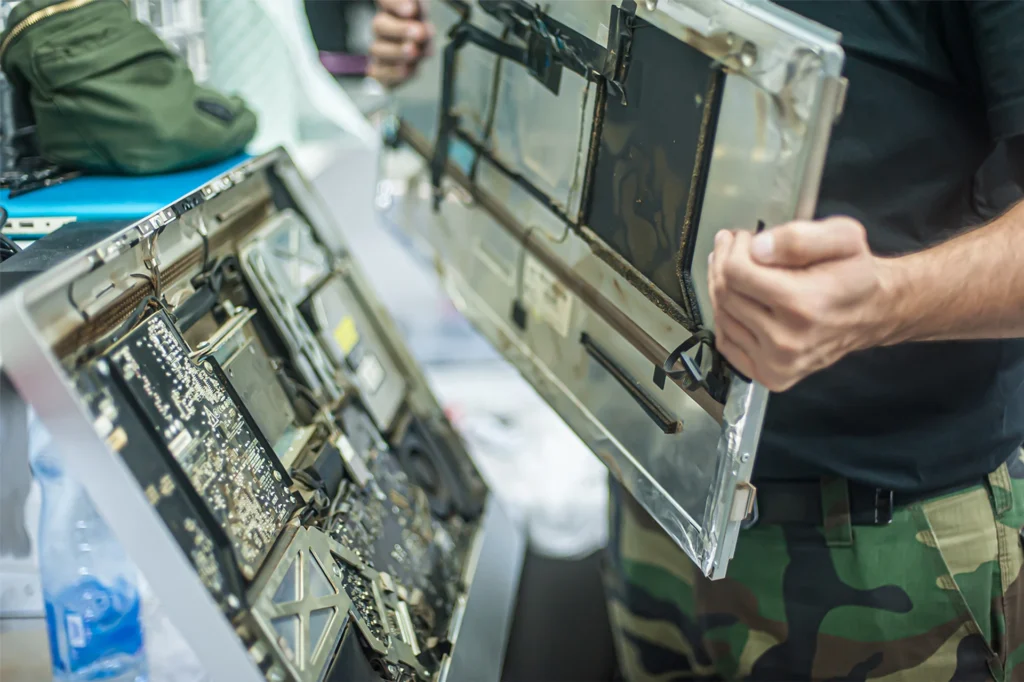
With the increasing digitization and automation of military systems, the demands on electronic assemblies in terms of resilience, miniaturization, and electromagnetic interference immunity are growing. Tresky GmbH, a leading provider of precision solutions for semiconductor assembly, specifically addresses the performance requirements of the security and defense industry with its DIE bonder systems and manufacturing services.
Tresky Automation presents contract manufacturing for small and medium quantities at PCIM
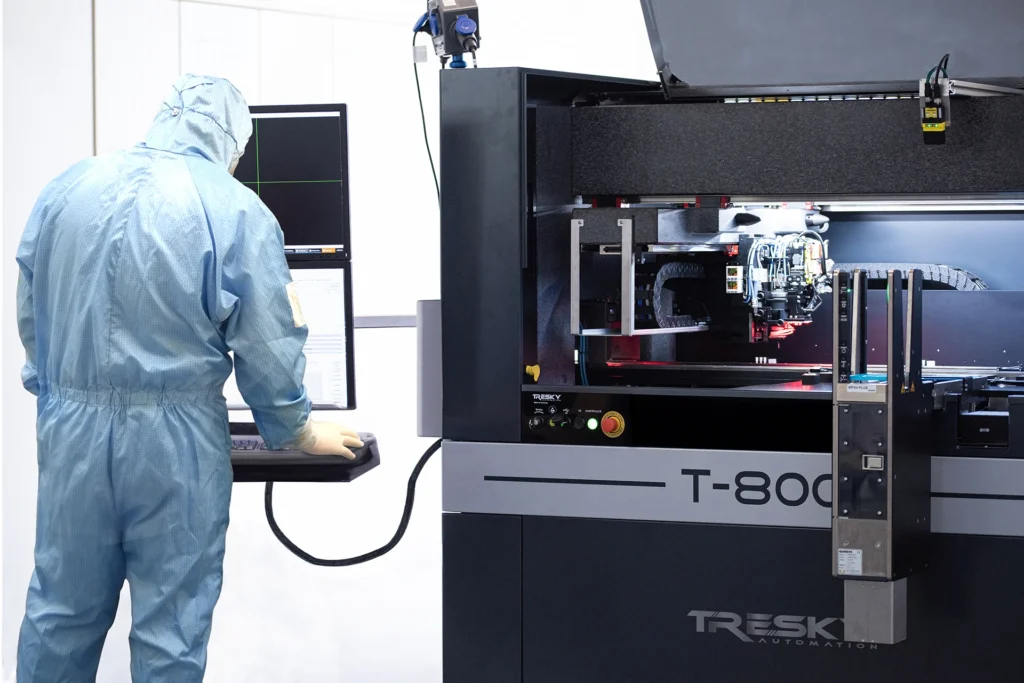
Tresky Automation will present its new contract manufacturing service for packaging at PCIM 2025. This innovative service offers customized solutions for various areas, including photonics, optoelectronics, sintering for power electronics, flip chip bonding, and many other assembly and connection technologies.
Tresky offers a wide range of application options for ultrasonic DIE bonding
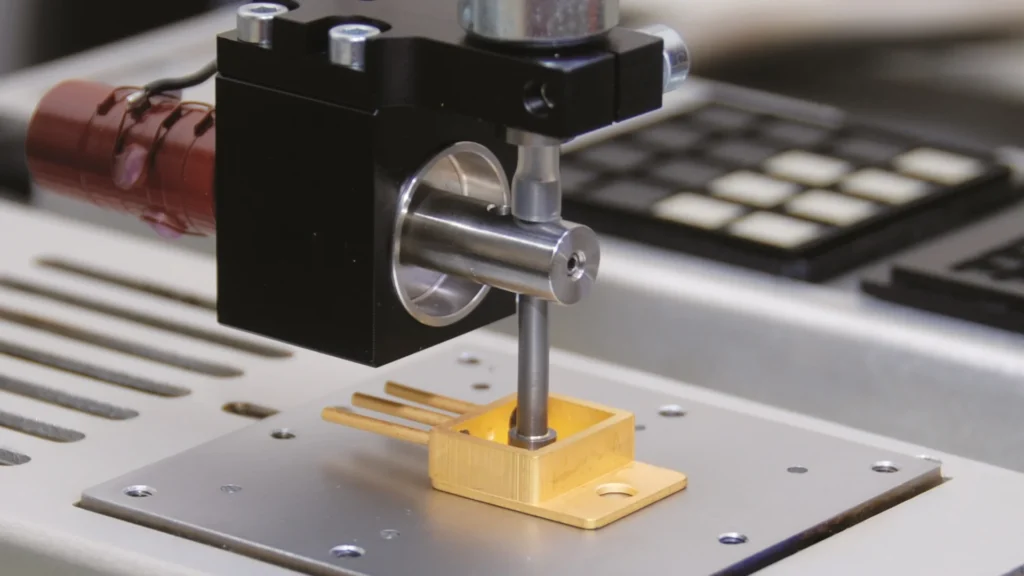
Ultrasonic DIE bonding is a fast, clean and efficient technology increasingly utilized in the semiconductor industry for the assembly of heat sensitive microelectronic DIE’s. This method leverages high-frequency ultrasonic vibrations to create a reliable bonds between semiconductor DIEs and substrates, significantly reducing thermal stress. The advantages of ultrasonic DIE bonding include rapid processing times, low temperatures and excellent mechanical strength, making it particularly suitable for advanced applications such as RF components, MEMS and LED packaging.
Tresky Automation is strengthening its portfolio by investing in the contract manufacturing sector
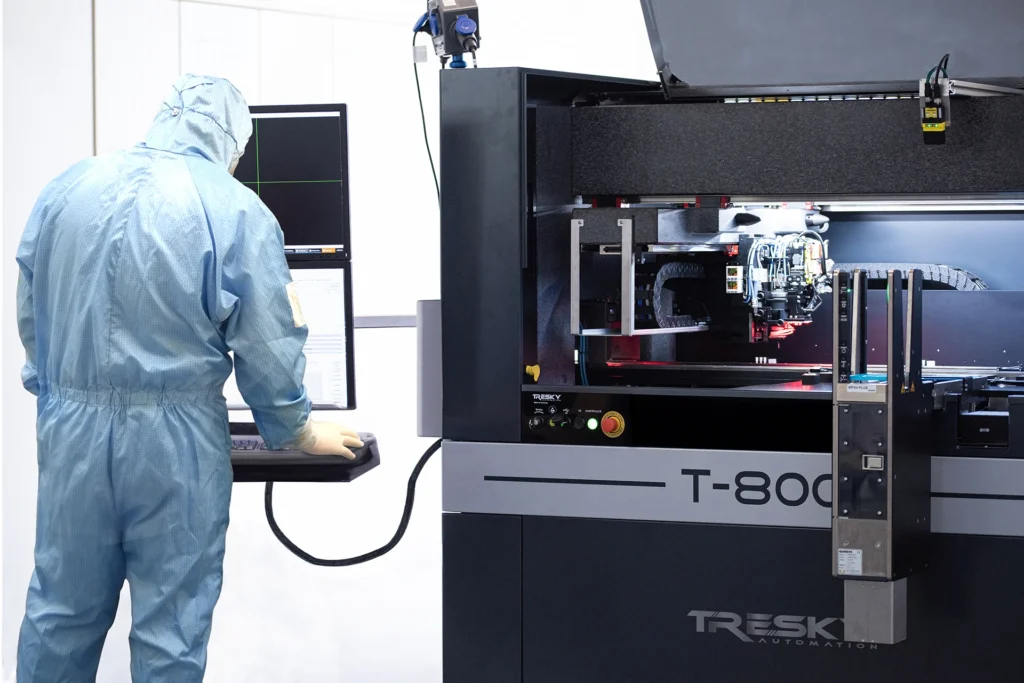
Tresky Automation is pleased to announce the latest addition to its machine park in the field of contract manufacturing. Customers will now benefit from a state-of-the-art vacuum soldering system and a high-performance sintering press with a maximum contact force of up to 15 kN.
ESCATEC pushes new boundaries in micro-electronics with UV enhanced die bonder technology
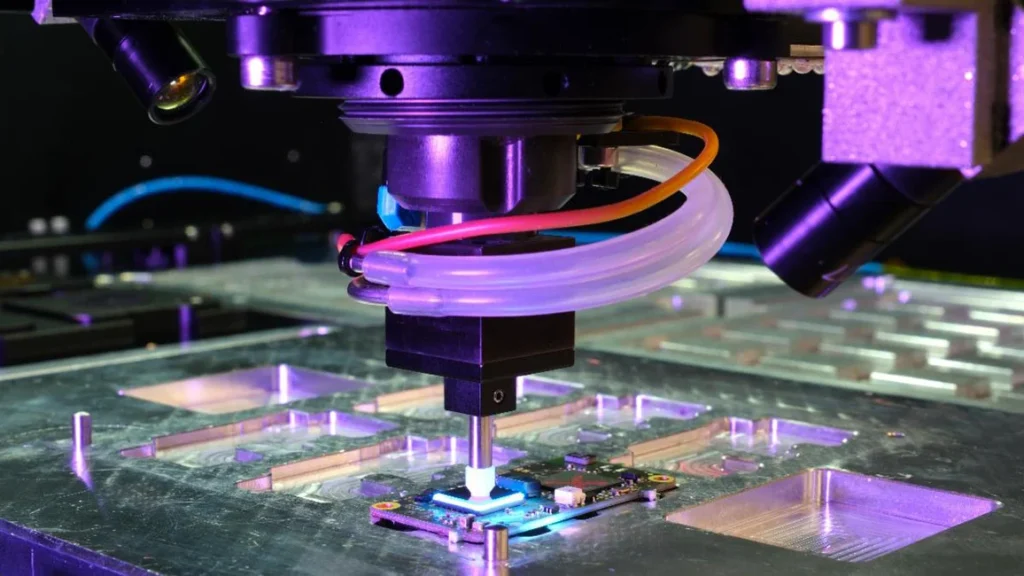
Electronics manufacturing services (EMS) provider ESCATEC has successfully integrated a UV light feature to its die bonder, significantly enhancing the precision and efficiency of the micro-assembly processes.
Laser- and photodiodes DIE bonding in optoelectronics
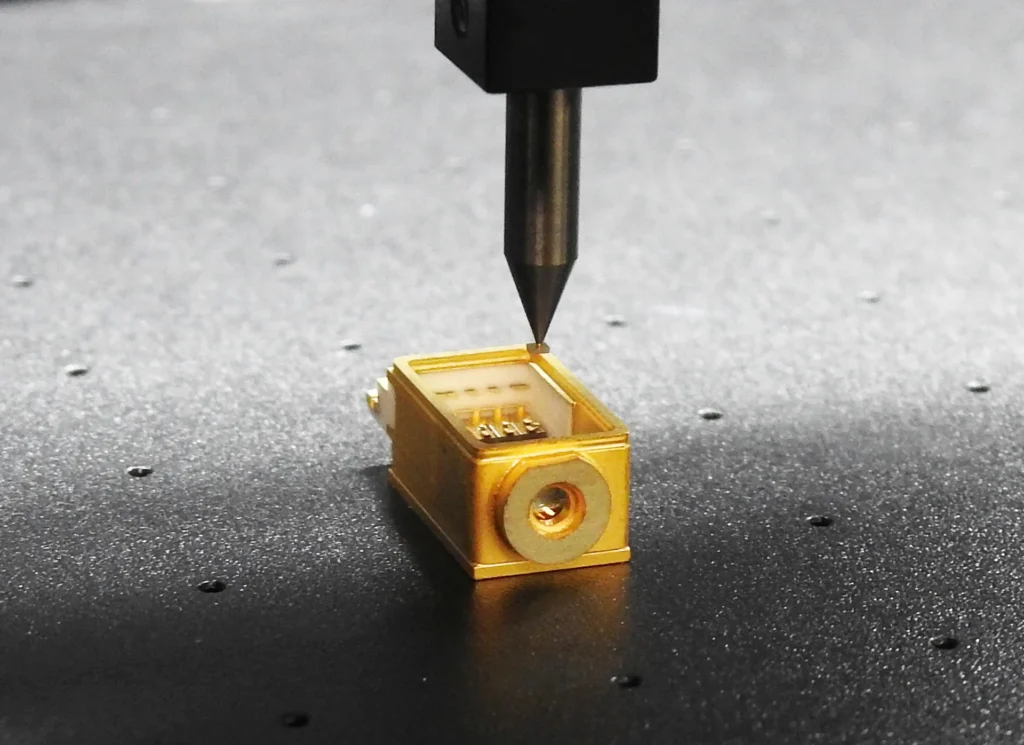
In the dynamic world of optoelectronics, where light and electronics come together, the connection technology plays a crucial role for the performance and lifespan of laser diodes (LD) and photodiodes (PD). Tresky GmbH, as a leading manufacturer of [bns_post_link id="4141" text="DIE bonding systems"], offers customized solutions that are specially tailored to the requirements of [bns_post_link id="4681" text="DIE bonding of laser- and photodiodes"].
Tresky offers DIE sorting as a contract service in semiconductor manufacturing
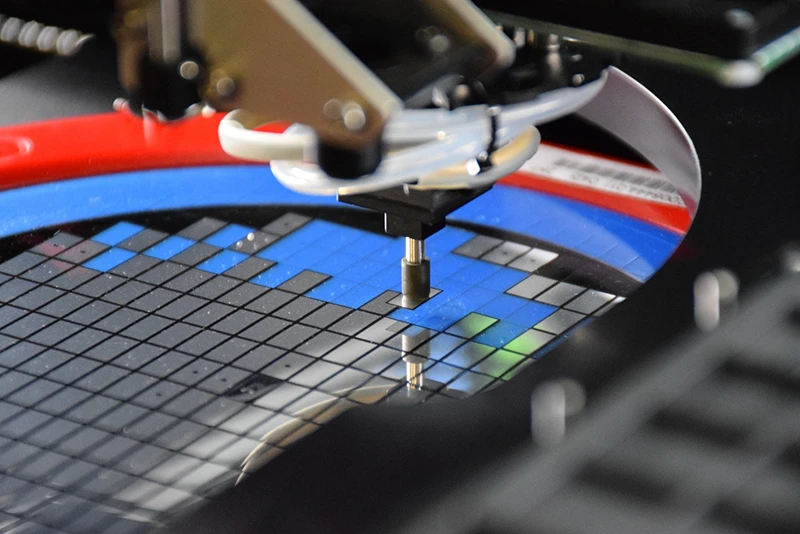
The Tresky Contract Manufacturing Hub offers more than just prototyping and small series production. We also provide DIE sorting for wafers up to 12″, along with semiconductor packaging services.
Tresky allows dispensing of over 100 mm² for large area sintering applications
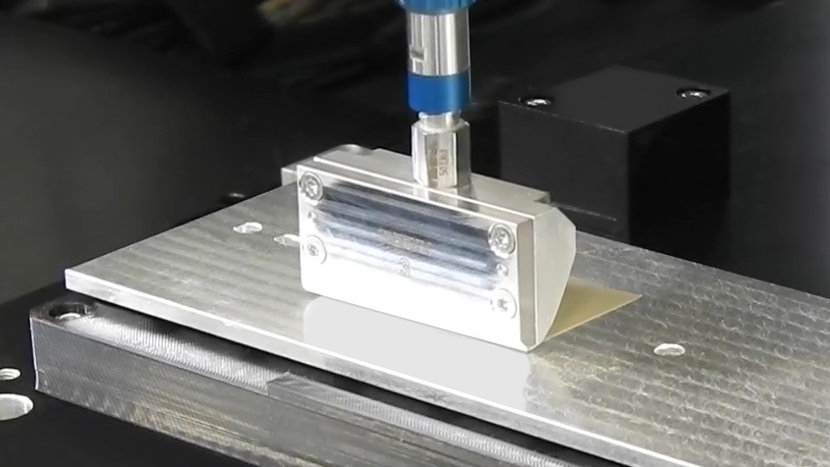
The integration of large-area power modules with an area of over 100 mm² is highly relevant. These modules are of great importance for various applications in e-mobility, as they offer high power density and efficiency. However, connecting these components is challenging. Tresky GmbH from Berlin is presenting dispensing for Large Area Sintering at PCIM Europe […]
Manual mode for maximum control and flexibility with DIE bonders
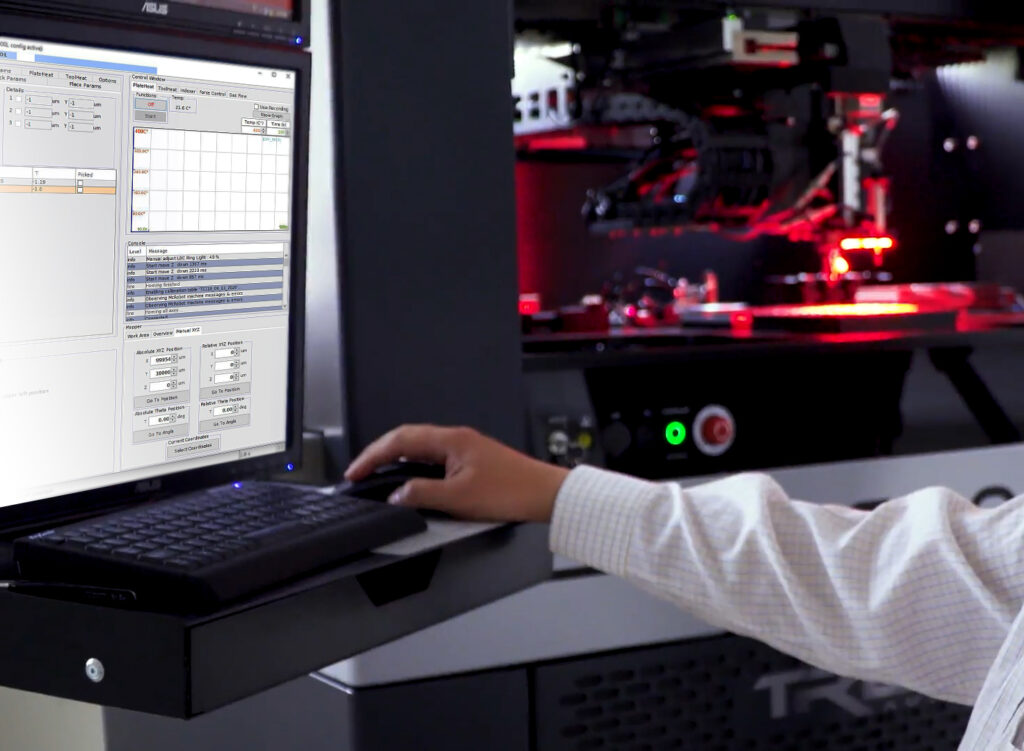
The DIE bonders from German specialist Tresky are equipped with a flexible, manual mode. This reduces the entry barrier for new users and makes it possible to achieve reliable die bonding results within a very short time. The manual mode is particularly suitable for applications that require quick iterations and adjustments while keeping highest precision. […]
Fluxless soldering using formic acid vapor for optoelectronics
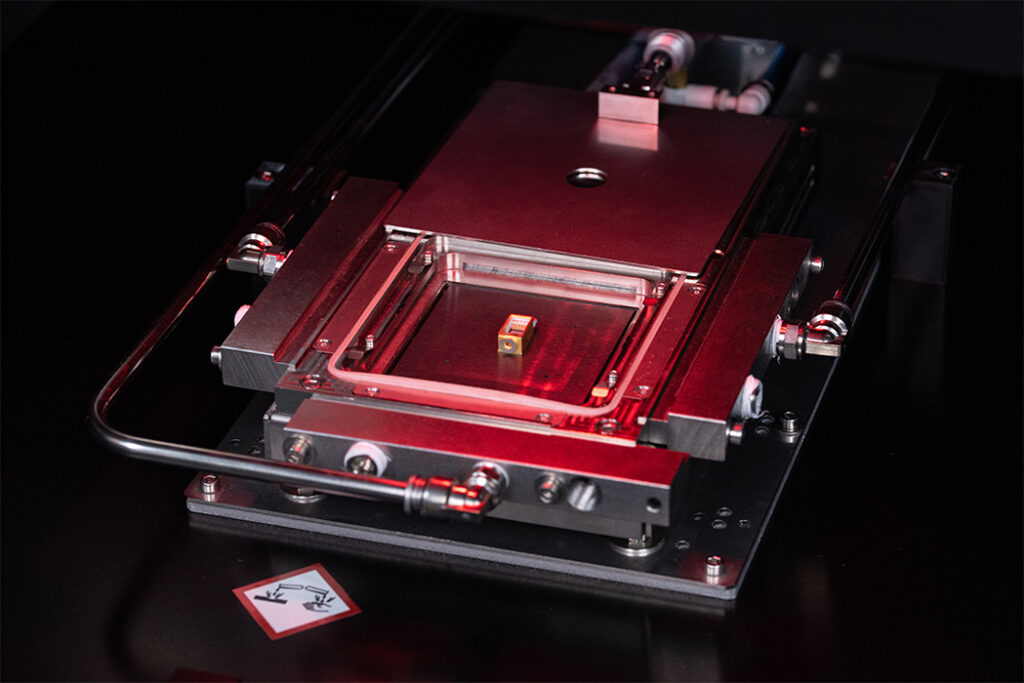
Soldering using formic acid vapor in combination with nitrogen (HCOOH + N2) offers significant advantages in assembly and connection technology for applications in optoelectronics and photonics. Especially in the field of sub-micron bonding, Tresky has introduced several innovations in recent months and is now presenting the formic acid module for reliable use in bonding processes at productronica 2023.